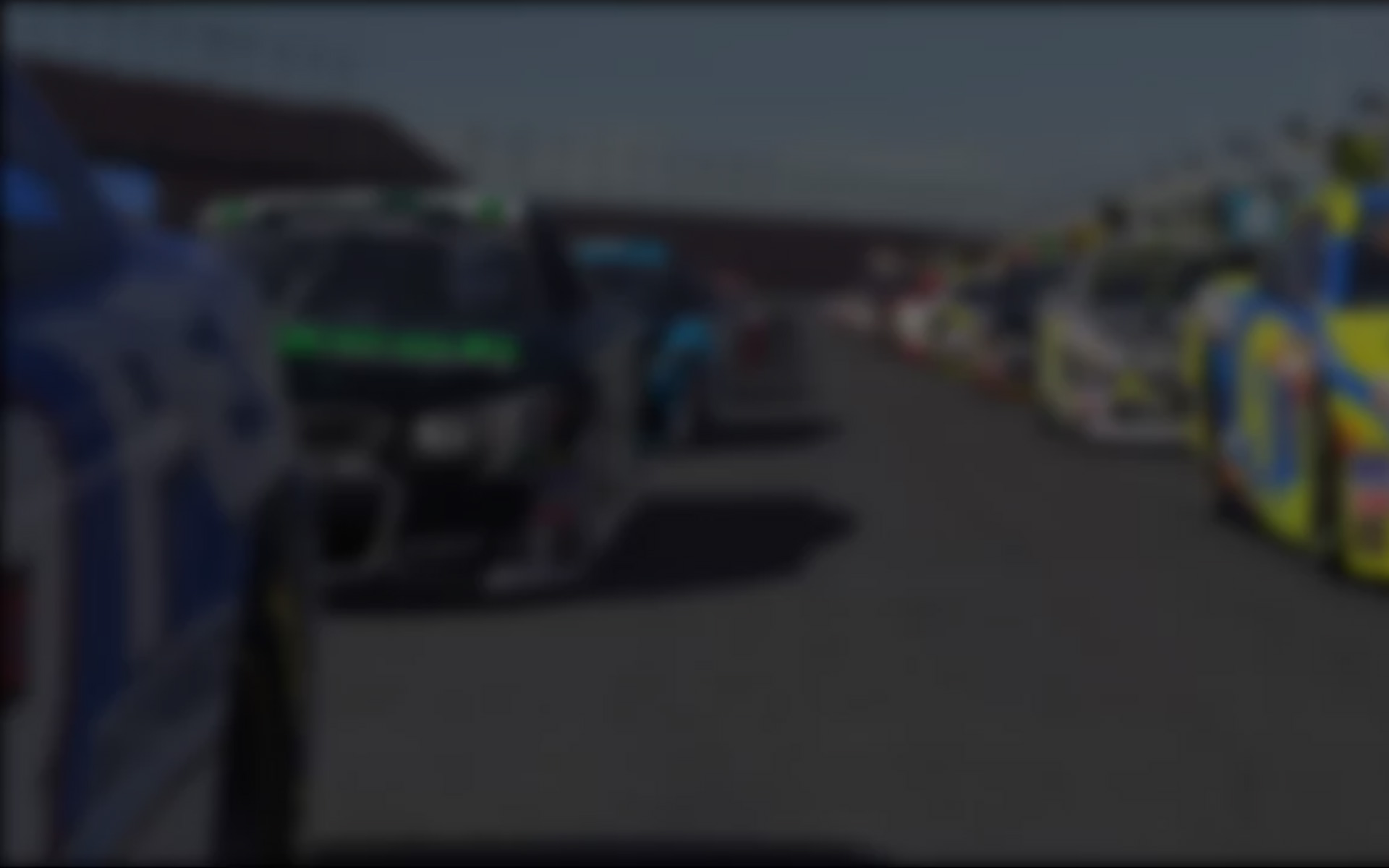
Behind the Scenes: The NASCAR Peak Antifreeze Series powered by iRacing.com – Sliders to Systems
September 27th, 2015 by JaimeB
Anybody remember this screen? If you don’t, shame on you. It’s the garage screen from Papyrus’ NASCAR Racing 2003 Season, probably one of the most viewed screens in sim-racing history. You can think of this screenshot as the great-grandfather of what we have today on iRacing. It represents a time when chassis setups were becoming more and more important to how well you did in a race. Was it realistic, though? Not, not at all. Being able to set up a winning car on sims such as NR2003 or any of the other racing sims of the time meant quite literally nothing in terms of being able to transfer that knowledge to a real car.
It wasn’t bad though, it made it easy for anyone to jump in and basically get their car where they wanted it to be. A couple of spring changes here, a few shock adjustments there, and voila! Those old garage screens (as well as the dreaded “Setup Matrix”) taught some very bad habits that can easily back you into a corner on iRacing. Whenever we get a new driver at Gale Force Racing, I always tell them the same thing to start off:
“Think of the older sims as having ‘Loose-tight’ scale from 1 to 10, 1 being ‘won’t turn in a 40-acre field’ and 10 being ‘could spin out on a railroad track’. The adjustments all had values that it would move the ‘Loose-tight’ scale in either direction. If you were super loose, just soften the right-rear spring a bunch. A little tight, just add a bit of left-rear rebound. Each driver had a point on the slider that, once they got there, their car was perfect. No matter what they did to get there.”
This is a gross oversimplification, but it is pretty straightforward at communicating the massive shift from NR2003’s garage system to iRacing’s garage system. There was almost no way you could get the car messed up in a mechanical sense, and one adjustment always had the same effect, regardless of the track, conditions, or other adjustments you may have made. As a result, the Setup Matrix began making rounds and anyone who memorized the Matrix basically became a Setup Wizard. One setup could be shared across a lot of drivers. That was the way of the times, we truly didn’t know much better.
Fast forward five years, and that system made it into the initial parts of the iRacing service. I remember a specific event during practice at Atlanta Motor Speedway in the Impala COT (back when it had the carbon-fiber wing) that almost made me cry…manly tears, of course. There was a setup “guru” in the session, whom I still have the utmost respect for so don’t start getting ideas, and he picked up a few tenths of a second on the practice chart. He keyed up the chat and told everyone what he did to his setup, and I saw 14 other cars go to pit road at the same time, leave at about the same time, and all pick up the same amount of time. Being able to share a setup across multiple drivers without issue was the story of the Impala COT’s entire life right up until iRacing’s “2.0” release. The one-setup-fits-all phenomenon continued for a while afterwards, however. In the early days of Gale Force Racing, where we ran our first Pro Series and then our first NASCAR PEAK Antifreeze Season, it was not uncommon for all four or five of our cars to run the exact same setup and all of them do well. The Loose-Tight scale has never been able to properly describe how iRacing’s garage worked, but in the early days it didn’t produce major issues when you made the wrong changes to the car.
Those days are all but gone now. There’s the question that’s asked every single time an update is released to the service: Why don’t we have an in-car track bar adjustment? I’ve wondered that too, but a forum post from one of the devs a few months ago cleared it up. He said that the track bar is modeled into the rear suspension systems, and changing the bar’s location requires the rear end suspension to be reloaded. This could cause the car to jump up into the air suddenly…and it’s very difficult to have any grip when you’re 30 feet in the air. Anyone who has backed their car into the wall and then sat on pit road for the repair knows what the developer was talking about. Personally, I think it would be cool if your track bar got adjusted on-track when someone hit your rear bumper. That would definitely increase passing!!
Anyway, that simple statement is big. It points out that the rear end housing and suspension for the NASCAR vehicles are treated as a completely modeled entity in the car. Each component in that system is modeled. Springs, track bar, truck arms, shocks, even torsion in the housing itself is modeled. Move up to the front of the car, where we know that it’s built similarly so that the front suspension is modeled by itself, and things get even more complex. On the NASCAR Sprint Cup car, we have main coil springs, secondary shock springs, shocks, a sway bar, suspension flex, and chassis torsion. In the suspension itself, there are a total of three spring rates applied to each corner of the car when it’s on track. There’s the main spring rate, then when it’s in contact we have the main spring and the secondary spring, and all that time we have a sway bar which is applying a torsion spring rate to the suspension as well. Add into all that the flex of the arms themselves and you could say we have four spring rates for each corner. Thank goodness we never got the pigtail springs that were used in the Cup Series, then we’d have five spring rates to make it even more complex.
It’s this complexity in the chassis modeling that makes our iRacing garage much more realistic than the NR2003 garage. Also, it’s this complexity that can cause major issues with chassis setup. In 2007, the Subaru World Rally team went into a performance freefall with their new car, unable to get any speed or handling out of the car for any of the rally events. The entire season was documented in a miniseries, and it was eventually discovered that bushings for the rear lower suspension arms prevented proper movement of the suspension, resulting in a car that didn’t behave as expected or responding to any changes as anticipated. We ran into a virtual equivalent to this in the 2013 NASCAR PEAK Antifreeze Series where we had a specific combination of track bar angle and rear spring package effectively “locking” the rear end of the car and preventing the suspension from working. Because of this, no wedge adjustments worked at all during the race, since adjusting the perches themselves had no effect on the car. In a nutshell, we’d broken the car completely. A bit of numbers jumbled together in the proper configuration turned the suspension into a solid entity, and it wasn’t really discovered until 2014.
This was the first time we’d seen any evidence that one adjustment would directly affect the rest of the car, and it was the first time we were aware that the cars were not the solid bricks from older racing sims, but a working system with many different parts, and each part had to be put together in the right way for it to work properly on track. Sure, the setup matrices were made completely useless with the advent of bumpstops and more sophisticated aero models. With bumpstops, front springs could do one of four different things depending on where they were in travel, and similarly the rear springs would do one of four things depending on how the aerodynamic attitude of the car was set. That’s great, and it’s been well known in real-world racing for a very long time, but it was the first time I’d seen something like that modeled into a simulation for public use.
This principle of an entire car working as a bunch of smaller parts is exactly what bit us in the Chicago race last week. We’d carried the setup from Darlington to Chicagoland (this time setting the track conditions properly!) and it was good right out of the gate, and some adjustments to fit it to the track made it better. Maybe not front runner pace, but way better than it was at Darlington. However, a rear spring change just before the race erased any hope of doing anything. We had all our adjustments arranged and planned with a specific rear spring split, a specific track bar angle, ride heights, pressures, etc. When the rear spring was changed, we did not change anything else to compensate for the new spring, and effectively made every single adjustment we’d made to the car in the past week useless. It was a different car, the dynamics were different, and sadly, we didn’t catch this misstep until after the race. As it turns out, as Nick was going through the corners, it’s very likely that the track bar angle was swapping between right-side-high and left-side-high as he was going over bumps through the corner, which is a huge problem. Similarly, the car was twisting and jumping under loads, turning it into more of a featherless dart than a racing car. As a result, he crashed after 68 laps of trying to wrestle a car that would not cooperate.
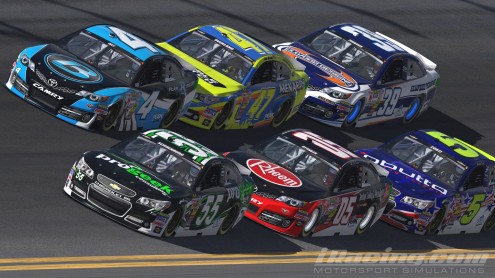
The setup in the GFR cars at Daytona (#4, #05, and #39 in shot) was the first setup built from the top down using real-world principles and it worked surprisingly well.
Chad Knaus one said something on NASCAR Performance that I believe should be printed in every setup guide ever created, and it was such a simple quote: “The springs, shocks, swaybars…all that stuff in the car is a package. It all works together, nothing works alone.” In the older days of sim-racing that wasn’t the case, and even up as recent as 2012 that wasn’t the case. We’re starting to move away from what we had and what is real, which is a car that is treated like a car, not just a box with some numbers on it. This year is the first year at GFR that the cars have all had differences in setups, some completely different setups altogether. Even when we raced and won the 24 Hours of Daytona, a few of us had to learn to race with a setup that was fast, but didn’t agree with us, myself included. The car didn’t work for me, but when the whole team was considered, it was better to go with a setup that more people liked and were fast with, and I simply just did my best to maintain our position overnight, and it worked.
There’s nothing wrong with that, though. Driving styles are different, and we see setup differences across two cars from the same team in the real world. Even the Joe Gibbs Racing cars, which are quite good this season, are far from the same. They can still use the same notes to build equal cars, however they just go about it different ways. A few spring changes, maybe a different shock build, and Matt Kenseth’s car would be a different setup than Kyle Busch’s car, but they still both do the same thing.
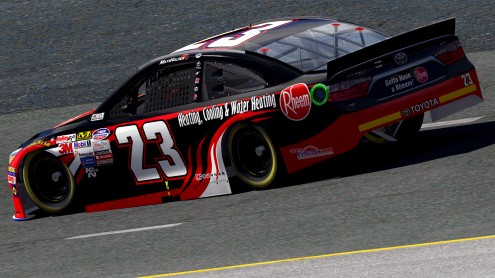
Our New Hampshire car for NiS was built using data from Chicagoland, principles from Daytona, and methods from the real-world. It was one of the fastest cars in every race it participated in, regardless of which split it was in.
Taking this new way of thinking into account, we’ve managed to produce two cars this year that were built from the top-down using real-world principles and achieved impressive results. The first was at Daytona in the NPAS series, where the car was built specifically with aerodynamics in mind. It led laps, it marched to the front, it did what it should have done.
The second? Just this week, Alex Scribner and I got together and built a car for New Hampshire using the same ideas used to build the Daytona car. We knew where we wanted to end up, how the car needed to look and feel, and built the setup meticulously in the way we would have approached a real car. The springs controlled the aerodynamics, as in real life. Weight was used to tune handling, as in real life. Shocks, alignment, even preloads were all used to fine-tune and get the car where it needed to be. Sure, some things weren’t exactly realistic because of a few physics issues, but it’s close. The results were impressive and unexpected. In our respective races, we were both the fastest cars on longer runs, and were the only cars able to pass on the bottom of the track while holding off cars who tried to pass on the bottom.
But the really impressive part is that our cars were not exactly the same. The only thing that was common across the two cars were the four main springs and the sway bar configuration. Everything else was changed slightly to fit our respective driving styles. Just like in the real world.